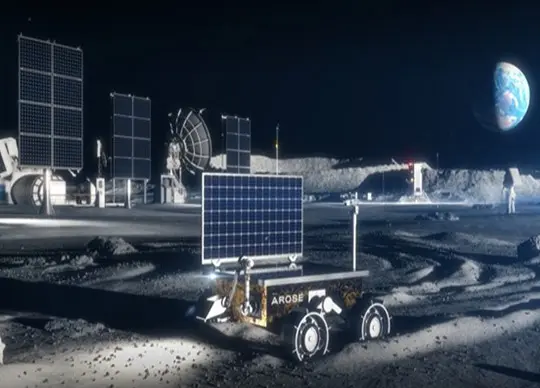
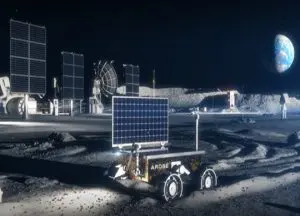
Artist’s impression of the NASA Moon base with the AROSE lunar rover in the foreground. Image courtesy AROS
When Australia’s Trailblazer lunar rover arrives on the Moon, the remotely operated vehicle will confront some of the most extreme environmental conditions ever encountered.
Because it lacks an atmosphere, the Moon undergoes large swings in surface temperature – from a daytime average of 123o C to -233o C at night. The lack of atmosphere, plus the absence of an electromagnetic field, also means the Moon is continually inundated with solar and galactic charged atomic particles.
Lunar soil, known as regolith, is vastly different to the soil found here on Earth. The physical properties of lunar soil are primarily the result of the mechanical disintegration of rock, caused by the steady bombardment of meteorites over billions of years.
The regolith is also composed of glass-like silica to form a sharp, unforgiving surface covered with a thin layer of electrically charged dust that sticks to any surface with which it comes in contact.
The lunar rover design will need to overcome these extreme conditions as it undertakes its mission for NASA – to collect soil samples and deliver them to a NASA processing facility on the Moon. NASA’s primary objective is to extract oxygen from the soil in situ as a critical step to establishing a long-term human presence on the Moon.
NASA has chosen Australia as its strategic partner to design and build the lunar rover due to our proven expertise in remote operations, developed through our world-leading resources industry.
The Australian Space Agency has tasked the AROSE consortium with developing the preliminary design of the Trailblazer lunar rover by the middle of 2024. If successful, the AROSE team – led by Fugro and Nova Systems – will then build, test, deploy and operate the rover on a future Moon mission for NASA as part of the Artemis program.
AROSE Director of Space Programs Dr Newton Campbell said the extreme environmental conditions on the Moon’s surface create specific challenges for the rover design.
“Lunar regolith is pretty nasty stuff,” Dr Campbell said. “It’s not like digging up normal dirt here on Earth. Since the Moon has no atmospheric or liquid erosion properties it’s much sharper than soil particulates here on Earth. We’re just not used to dealing with that, even with what we deal with in the Pilbara.”
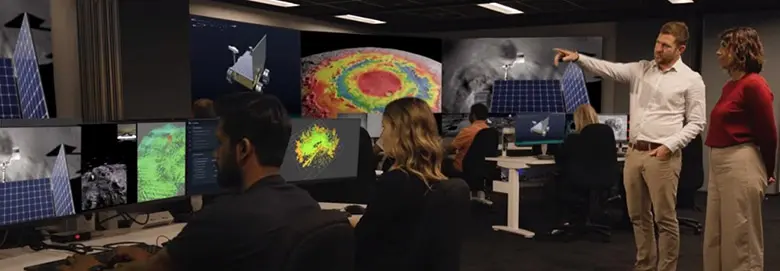
Located in the heart of Perth’s central business district, Fugro’s Space Automation, Artificial Intelligence and Robotics Control Complex (SpAARC) will test, train and control remote and autonomous operations for future Space missions.
Dr Campbell said there would be a significant amount of advanced tech in the rover design.
“Everything you’re building for Trailblazer is almost entirely new because you have to make these technologies Space-grade,” Dr Campbell said.
“That means they must withstand extreme temperature variations. Not just built for the hot, not just built for the cold, but built to deal with both of those things, with new forms of shielding for example.
“The rover’s onboard sensors will need to detect those variational shifts in temperature, and potentially modify the robot as the temperatures are swinging.”
Dr Campbell said command and control of the semi-autonomous rover from Earth would be subject to varying amounts of real-time delay.
“When you’re talking about the Moon, you could be talking about several seconds delay simply due to the distance from Earth. Additional signal problems can occur based on a number of factors, such as electromagnetic interference caused by solar radiation.”
In the case of the data path from the rover’s on-board sensors to the Earth-based control centre, these impacts can range from a potential increase in error rate to a total loss of data.
“So you have to introduce artificial intelligence capabilities that effectively help guide the robot in times of significant latency, to continue operation and make sure the rover is maintaining its own safety, as well as with respects to the environment.”
If the AROSE rover design is accepted for the Moon mission, its operations will be remotely coordinated from Fugro’s newly built Australian Space Automation, Artificial Intelligence and Robotics Control Complex, better known as SpAARC. Located in Perth’s central business district, this world-class facility is a joint initiative by the Australian Space Agency, Western Australia Government and Fugro.
Fugro Space Systems Director Dawn McIntosh said the size and weight restrictions placed on the rover by NASA create challenges for the on-board navigation system.
“At no more than 20 kilograms and approximately 50 centimetres square, little things like small rocks become big things,” Ms McIntosh said. “Bigger rovers can ignore small rocks, we can’t.”
The best place to locate a Moon base is the lunar south pole, which has large reserves of water in ice. This is where NASA plans to set up home on the Moon.
“Australia’s lunar rover will play an important role in determining the long-term viability of NASA’s Moon base,” Ms McIntosh said. “This is a critical step toward a similar base on Mars, and beyond, in the decades to come.”
Resource industry heavyweights and AROSE members Woodside and Rio Tinto are contributing to the lunar rover effort by providing knowledge transfer of their terrestrial robotic and automation capabilities.
“Australia is already the world leader in remote operations for the mining sector,” Ms McIntosh said. “Now we are well positioned to become a leading provider of remote operations technology and expertise for Space.”