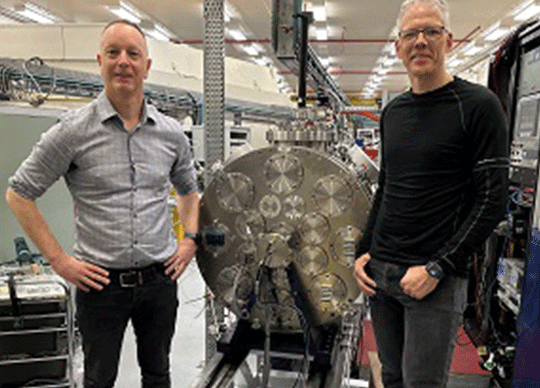
Cost can be a huge barrier for Australian companies to reach low Earth orbit (LEO), with payloads billed per kilogram of weight by launch providers.
At the same time, structures need to be robust to survive launch and operations in the extreme and harsh temperature environments of space.
The next iLAuNCH Trailblazer project aims to reduce weight in satellites through the additive manufacturing of lightweight and thermally stable composite structures that will ultimately save on the cost to access space.
Teaming up with The Australian National University and industry partner New Frontier Technologies, this Trailblazer project will develop a material solution based on carbon fibre.
“This first Materials and Processing commercialisation project will develop protective coatings for carbon composite components that will be deployed in space environments for long durations,” said iLAuNCH Trailblazer Executive Director, Darin Lovett. “We are developing world-class sovereign manufacturing capability that is cost competitive and utilises the latest advancements in materials; vital for realising the full potential of an Australian space manufacturing industry.”
In LEO, spacecraft are exposed to a range of environmental hazards that can damage their structural integrity, including UV irradiation, atomic oxygen, high energy particles, and space debris.
These environmental hazards can cause surface erosion, cracking, and delamination of composite materials, which can lead to a reduction in the mechanical properties of the material and can compromise the structural integrity of the spacecraft.
The project will leverage material research capacity in the Research School of Physics at the Australian National University; including nanomaterials fabrication and characterisation, x-ray computed tomography (CT) imaging, and space testing capability at the Australian Advanced Instrumentation Centre (AITC) at Mt. Stromlo.
“The target applications are satellite structures such as struts, booms and reflectors. The primary aim of the project is the development and validation of carbon-fibre/thermoplastic composite structures for these applications with coatings that provide improved radiation shielding and resistance to atomic oxygen degradation,” said New Frontier Technologies Director and CEO, Paul Compston. “We will develop coating application methods that are compatible with our automated composites manufacturing technology to produce structures that are lightweight, to help to reduce launch costs, and have added protection once deployed in the harsh space environment.”
The coatings will be based on nanomaterial technology developed using the expertise of ANU.
“We are pleased to partner with New Frontier Technologies,” said the Australian National University’s Research School of Physics, Professor Patrick Kluth. “We will use our expertise in nanomaterial science and characterisation capabilities to develop and optimise robust coatings that meet performance requirements for space applications.”
“The strength to weight ratio of these materials will allow a substantial reduction in mass which is a fantastic benefit to space applications,” said New Frontier Technologies Director and CEO, Paul Compston.
This activity will demonstrate innovative nanomaterial technology, novel designs for increased structural efficiency and rapid precision manufacturing of satellite components with a huge cost benefit to decreases in weight while maintaining technical performance.